Tape Caster
Supervisors : Elisa Mercadelli, Paola Pinasco
Tape casting is a simple and versatile shaping technique that allows the production of planar sheet of ceramic or other materials with thickness ranging between 30 µm to 1.5 mm.
The process can be divided in different steps:
• preparation of the powder suspension with suitable organics (deflocculants, binders, plasticizers, surfactants) in a solvent (organic or water);
• filtration;
• de-aering (elimination of air bubbles included during mixing);
• tape casting;
• drying;
The final thickness of the tape is determined by adjustable blades (regulated through micrometer screws). The suspension is poured into a distributor (“doctor blade”) positioned upon a movable polymeric carrier. When the latter is put in motion, the suspension passes under the blades to give a wet sheet of determined thickness. Afterwards, the as-cast wet sheet reaches a closed chamber where the solvent evaporates to obtain flexible green tapes.
In particular, this casting bench is able to supply tapes with a maximum width of 20 cm and a length of more than 3m, with thicknesses that can range from 50 µm to 1 mm.
The product thus obtained, after appropriate thermal treatments of “de-bonding” and sintering, gives rise to multi-laminates which can be of functional gradient or combinations of different materials.
This process allows to obtain flexible green products of high area and low thickness that can be easily cut (punched) and then stacked. Tape casting is in fact the main technique for the production of multilayers for electronic and energetic applications.
The process consists of the following steps:
• punching of the single tapes;
• stacking;
• lamination (parameters: temperature, pression and dwell time).
The optimization of the necessary thermal treatments (de-bonding and sintering) leads to a final functional graded product or a multilayer that can couple different materials.
Some examples produced in ISTEC are:
• Alumina (Al2O3) / Alumina+zirconia (ZrO2);
• Piezoelectric materials (PZT, PZTN);
• Na-β-alumina membranes;
• Non oxide ceramics (AlN, MoSi2, SiC, B4C);
• Elements for Solid Oxide Fuel Cell/Electrolyzer aplication (SOFC). Fuel electrode: NiO/(Zr,Y)O2, NiO/Ce8Gd0.2O2, NiO/Ba(Ce,Y,Zr)O3, (Sr,La,Ti)O3, (La,Sr,Cr,Mn)O3; Electrolyte: (Zr,Y)O2, (Zr,Sc)O2, Ce0.8Gd0.2O2, Ba(Ce,Y)O3, (La,Sr,Ga,Mg)O3; Oxygen electrode: La0.6Sr0.4Fe0.8Co0.2O3 (LSCF), La0.8Sr0.2MnO3 (LSM), LSCF-GDC, LSM-YSZ, LSM-GDC; Metal substrate: Ni, Stainless steel.
Typical examples of this kind of multilaminar structures are:
• Solid oxide fuel cells (SOFC) and electrolyzers (SOEC);
• Asymmetric ceramic membrane for hydrogen or oxygen separation;
• All-solid state ceramic batteries;
• Porosity graded piezoelectric systems for ultrasonic applications;
• Composites with enhanced mechanical behavior.
List of equipment available for the process
• Tape caster;
• Mechanical roller mixer;
• Deaeration Systems;
• Punch press;
• Thermo-compression system.
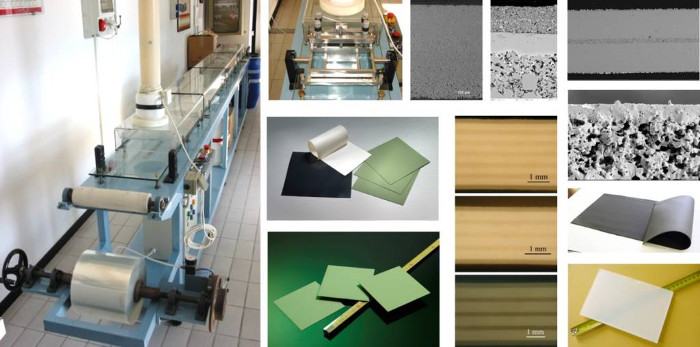