Extruder
Supervisor : Alessandra Sanson
Extrusion is a shaping process used to produce long, straight, semi-finished products of constant cross section.
The principle is very simple: under a high load, a plastic mixture is squeezed from a closed container through a die to give a reduction in size. Cross sections of varying complexity can be extruded depending on the material and the dies used.
The mass in the extrusion chamber is compacted and the green products is then cut to the desired length. The process itself is very simple but requires optimization of the paste to prevent the occurrence of complications during the process and defects in the green bodies.
ISTEC uses a vertical extruder that allows the processing of few kg of product. Differently from the normal horizontal continuous process, this geometry allows a better space organization and the production of reliable lab-scale products.
The paste is made by ceramic raw materials with the addition of appropriate organic additives (plasticizers, binders and lubricants) in aqueous system using a mixer with sigma rotors (battagion) at high shear. The mixer chamber is water-cooled to avoid temperature rise and subsequent evaporation of the water that can affect the mixture properties. The so obtained mixture is then placed into the filling chamber of the extruder and the upper piston squeezes the paste through the die.
A very important issue is the drying of the extruded products: these are placed in rooms at controlled humidity and temperature, and dried very slowly to obtain crack-free specimens.
ISTEC has long experience in producing:
• Rods & cylinders,
• Tubes,
• honeycomb structures, of different materials (TiO2, Al2O3, Cordierite, Perovskyte, ecc) especially for catalytic applications.
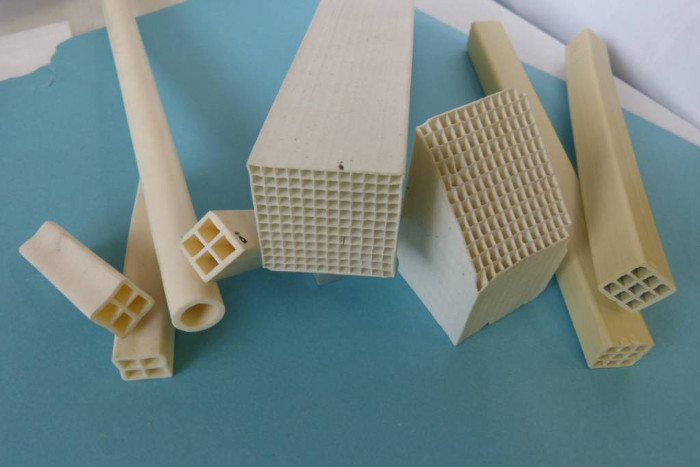