This website uses cookies so that we can provide you with the best user experience possible. Cookie information is stored in your browser and performs functions such as recognising you when you return to our website and helping our team to understand which sections of the website you find most interesting and useful. More information in our Privacy Policy
Spray-dryer
Supervisor: Anna Luisa Costa
The spray-dryer allows the transformation of aqueous liquid solutions or suspensions into powders, through an atomization process. The spray-drying process involves atomizing the concentrated feeding liquid into small droplets inside a chamber where hot air circulates, with consequent instant evaporation of the water. This process is ideal to guarantee the conformity of the final product to specific quality standards relating to the particle size distribution, residual humidity, apparent density and particle shape. The process is widely used as an encapsulation technique for active phases (as nanoparticles, drugs or catalysts) in a (polymeric or ceramic) support matrix. At an industrial level, as well as on a laboratory scale, the spray-drying process is used in various sectors, the main are chemical, ceramic, agri-food and pharmaceutical sectors. In the field of nanotechnology, this process is exploited to obtain nanostructured micrometric granules, starting from nanosuspensions (“from nano to micro” technology). This allows a significant safety advantage by avoiding the handling of nanometric powders.
Principle of operation
The spray-drying process begins with the atomization of a liquid material in a droplets nebulization. The feeding of the material to be processed takes place via a peristaltic pump, at the same time an air jet generated by an air pump with integrated compressor causes the liquid coming out as a fine spray through a nozzle. The droplets come into contact with the air, which can be in co-current or counter-current (recommended as it favours the drying process) with respect to the nebulization flow. This takes place inside the drying chamber, with consequent evaporation of the liquid and formation of dry granules. The evaporation of moisture from the droplets and the formation of dry granules takes place under controlled conditions of temperature and air flow, while the powder is continuously discharged from the drying chamber, through a cyclone. The dry powder obtained consists of micrometric granules with a 5-50µm size range, depending on the feed material and the set process parameters.
Main characteristics
The unit is designed to ensure that all functions are simple to select and adjust, to quickly achieve the optimum conditions for spray-drying. The control panel includes:
- inlet temperature setting and digital display of actual temperature;
- outlet temperature with digital indication;
- on/off switch and indicator for all systems;
- on/off switch and indicator for blower;
- blower control (operates a butterfly valve in the air inlet);
- on/off switch indicates for heater (this will not operate until the blower is switched on);
- on/off switch and indicator for compressor;
- compressor air flow valve control;
- automatic jet de-blocking frequency control knob (operated by integral compressor);
- on/off switch and indicator for Pump
- Pump Speed Control.
Lab Plant SD-05
- Evaporation rate of water at inlet temperature of 250°C using Standard Chamber: approximately 1500 mL/hour.
- Air inlet temperature range: 40°C to in excess of 250°C.
- Drying air throughput: variable from 38 to 73m3/hour.
- Heater capacity: 3 kW.
- Compressor: 1.4 m3/hour at 1.0 bar to 0.25 m3/hour at 4 bar.
- Sample feed: peristaltic pump with flow rate variable up to 65 mL/min.
- Jet de-blocking: integral 3 bar compressed air supply with variable de-blocking plunger frequency.
- Spray system: 2 liquid nozzle with standard 0.5 mm jet and options of larger diameters.
- Spray/hot air flow: co-current or counter-current.
- Power supply: 220/250 V – 50/60 Hz – 13 A.
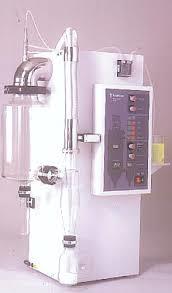