Electric furnaces
Supervisor: Alex Sangiorgi
The ceramic materials consolidation, whether traditional or advanced, takes place through the application of high temperatures and, in some cases, particular atmospheres (gas or vacuum). In particular, if during heating there is a liquid phase formation, mostly glassy phase, we have the so-called liquid phase sintering, typical of traditional ceramic materials. On the other hand, if the ceramic powders gradually start to consolidate and densify avoiding a liquid phase formation, we can speak about solid phase sintering; the underlying mechanisms are attributable to the atoms diffusion and therefore to the mass transfer that occurs during the solid state reactions. This mechanism is typical of advanced ceramics. The thermal energy necessary for sintering can be obtained by direct transformation of the electrical energy, according to Joule’s law, after the application of an adequate voltage to the resistor/s (Kanthal, Superkanthal and graphite).
In ISTEC, electric furnaces are used for different purposes, from powders calcination to sintering, passing through debinding or thermal shocks made with elevator ovens.
Electric furnaces, Nannetti S.r.l. (Italy) and Nabertherm (Germany)
The electric furnaces in CNR-ISTEC allow to sinter a wide range of ceramic products. Their most important characteristics are:
- Minimum and maximum temperatures: 750-2100°C;
- Minimum and maximum heating rate: 10-600°C/h;
- Oxidising atmosphere or Ar and N2 flux;
- Variable heating chamber sizes up to 600x400x300 mm3;
- Temperature controlled by thermocouples or a pyrometer.
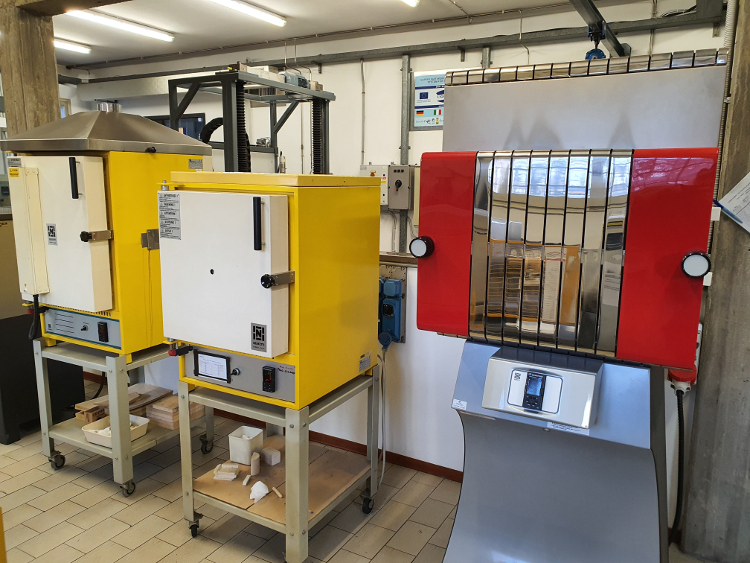